Brandauer stamps its presence in electrification laminations with £1m project
A stamping specialist is pressing the button on a £1 million project that will see it develop a new process to support the UK’s acceleration into electrification.
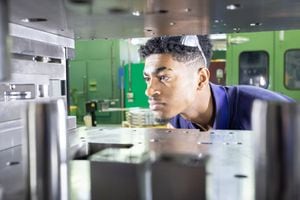
Brandauer, which already produces components for use in more than half of the world’s cars, has secured more than £300,000 of funding from the Industrial Strategy Challenge Fund run by UK Research and Innovation to help it set up a high volume e-machine stack line to produce thin laminates required by the automotive and aerospace sector.
Working in partnership with WMG and supported by Jaguar Land Rover, the 158-year-old Birmingham manufacturer believes there is an initial £500,000 opportunity it can secure once the methodology is in place, with the longer-term projections being of a marketplace worth between £60m and £70m.
Engineers and academic experts will be working to create an in-line adhesive dispensing process to support the volume challenge, whilst the second part will see them work towards the integration of an advanced stamping line capable of creating 0.1mm laminations with very narrow iron bridges.
“This project is a game-changer for our business, but importantly a game-changer for the UK power electronics, machines and drives supply chain and its ability to supply an increasing demand for e-components from tier ones and car makers,” explained Adam Burgoyne, new product introduction and quality engineer at Brandauer.
“Our laminations business is growing, initially focused on aerospace and defence work. However, the really big opportunity is in electrification and, to put us in that global arena, we need to be able to stamp extremely thin laminations to a high quality and large volume.”
He continued: “This is what we’ll be working towards over the next twelve months, bringing in the knowledge of WMG and the guidance of JLR. Taking on a project of this magnitude during Covid-19 is a big challenge and has been made possible thanks to the financial support secured from UK Research and Innovation.
Brandauer, which developed its own range of nose clips for face masks and a new visor to support the fight against Covid-19, will start by developing its own in-house methodology, transferring expertise from applying lubricant surface coatings to stampings during manufacture.
This will reduce the company’s cycle times, whilst also improving its productivity and allowing it to grow its capacity by 50 per cent.
The second stage will use the existing design of a rotor/stator stack with 0.2mm laminations as a base, before changing the material thickness to the required 0.1mm. Proving out stamping feasibility and preparing for manufacture will take place, with narrow bridge trials completed to identify the exact production process and the required state-of-the-art manufacturing techniques.
“There is a clear market signal, with our sales engineers regularly fielding £10m enquiries per annum for this capability,” added Mr Burgoyne.
“This isn’t just about Brandauer though. This is about creating a process and technology that will deliver the UK a vitally important technology, which will not only drive the sector’s growth in electrification but will also support the net carbon 2050 target.”
Brandauer produces millions of high tolerance metal pressings and stampings every week for customers in the plumbing, automotive, domestic products, electrical, medical and renewables sectors.
It is part of a new manufacturing cluster that has been established to target multi-million electrification opportunities over the next 12e months and includes Alucast, C-MAC SMT, PP Control & Automation and industrial automation specialist Balluff.