New designs set to increase UK face shield production
The University of Hull will share the designs, which use techniques such as laser cutting and injection moulding, to help prevent coronavirus.

A university is developing new face shield designs that can be mass-produced in minutes to try to maximise the supply of the life-saving equipment for healthcare workers across the UK.
A team of engineers at the University of Hull has worked around the clock to create the new designs, which can be produced by high volume manufacturing techniques, such as laser cutting and injection moulding, rather than 3D printing.
The techniques used to produce the designs, which will be shared nationally, could increase the amount of face shields made each day from 100 to up to 5,000.
The university is leading a collaboration to increase production of the face shields to prevent the spread of coronavirus in healthcare organisations.
After a request from NHS consultants, the team adapted designs shared by the engineering and maker community to suit their 3D printers and to fit with the feedback from medical consultants.
They delivered around 500 face shields in just four days but now aim to produce more than 20,000 products per week, using the industrial technique.
Nathan Brown, senior lecturer in mechanical engineering at the University of Hull and lead for this project, told the PA news agency: “3D printing is very good for making one-off parts but when you’re looking for mass production, it’s not really the technology that we want to be using.”
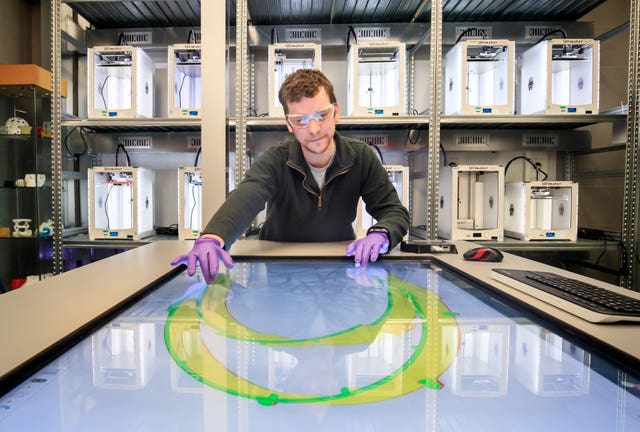
Mr Brown said they are now working with a local injection moulding company, who had taken the 3D printed model design and remodelled it to suit their manufacturing process.
He said: “Hopefully, within the next week or so, we should be in a position from that design that we can manufacture between 2,000 and 5,000 a day.”
And he said the team has developed another design based around technology – such as laser cutting, water jet cutting or stamping – to produce the product, which would also enable large numbers to be manufactured.
Mr Brown said: “The responses we’re getting, the feedback, is phenomenal really. They’re so appreciative of it and they’re so happy.
“The local community, because there’s been more people than just the university involved in this, they’re so happy that everyone is pulling together, demonstrating that we can really deliver a difference on this regional, and hopefully a national, level.”
He added: “We’ve had sources such as schools, colleges, local businesses, all offering up whatever they’ve got and we have a whole host of people who are lining up ready to help us and they want to see whether they can take any of our designs and use them.
“When we’ve finished this piece of work and hopefully get to a stage where we can really implement these designs, we’ll now share all of the design work that we’ve done with the national and international community so that they can take it and continue developing and use it in their regions.”
The university is appealing to any local businesses who can support the project – with either the supply of PETG materials or 3D printing, laser cutting, or water jet cutting equipment – to get in touch at fblp-business@hull.ac.uk